There are three primary reasons for drilling & choosing a carbide bur has its part.
Reasons for Drilling
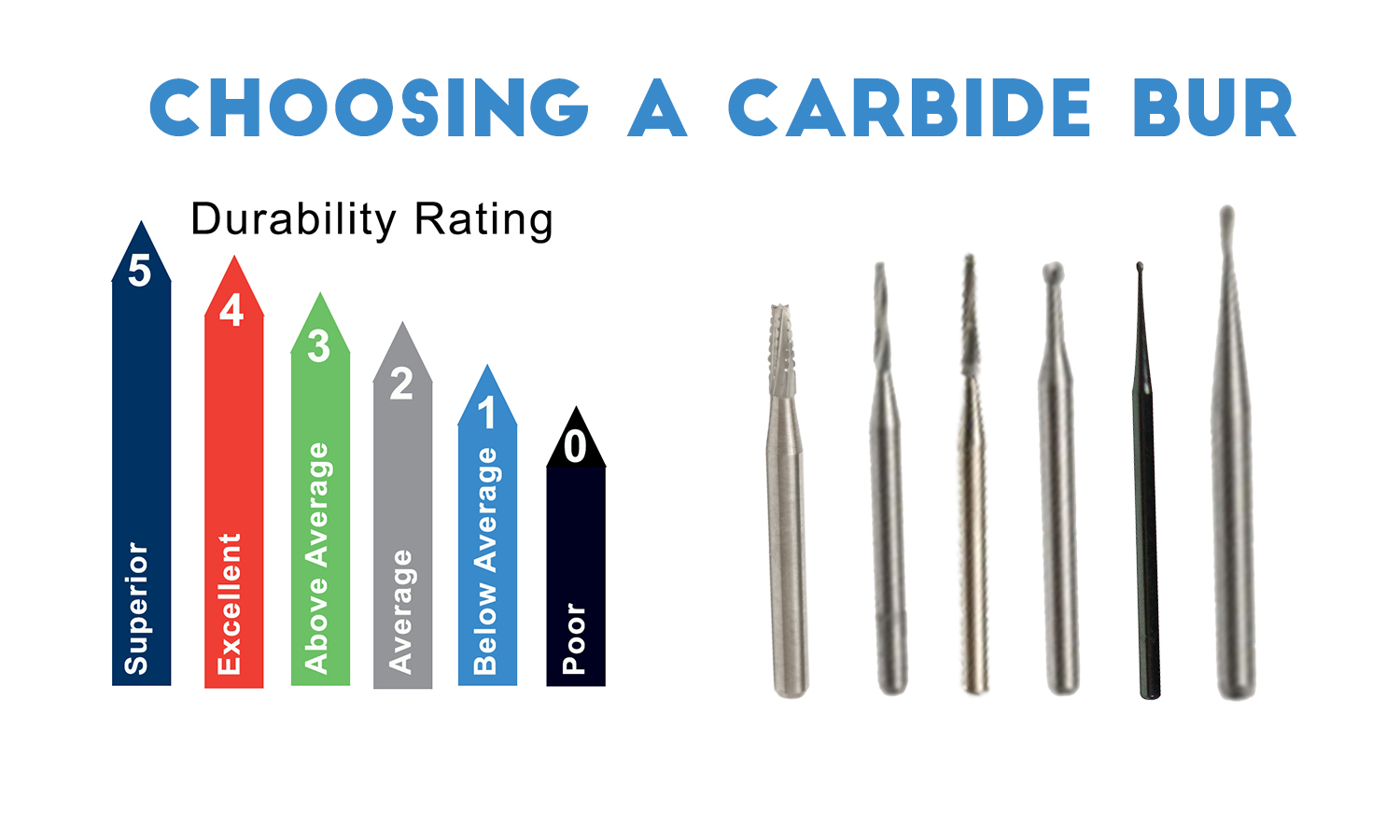
- Long cracks. Drilling the end of a crack over 3” long relieves some of the stress that can cause the crack to run during the filling process. After filling and curing the resin, the drill hole at the end of a crack adds stability and helps prevent future crack outs. It’s important to select a bur that matches up with the point size and shape of the slide hammer or spring hammer. The Delta Kits 26020 Tapered Carbide Bur is perfectly suited for this purpose.
- Sub-surface damage with no surface chip by which to access the damage. In this case, drill a hole through the surface of the glass and into the airspace below. A small bur is perfect for this purpose. Cosmetically, a smaller hole will look better after completing the repair. My preference is the Delta Kits 26030 Round Carbide Bur due to small size, durability and skip-free round tip, but we offer four other various shaped carbide burs that are as small or smaller depending on your preference.
- Capping a large pit. If the pit is too large to completely cover with the injector end seal, the easiest solution is to cap the pit with pit filler and scrape flat, then drill a small hole through the cap to access the airspace below. I really like the Delta Kits 26040 Pear Carbide Bur. It’s not quite as durable as the aforementioned burs, but it drills a tiny hole that is barely noticeable and because I’m only drilling through the resin, durability isn’t an issue.